公司致力于钢质管道防腐保温、管线施工新技术、新工艺及配套设备的研发,示范和推广应用。公司与中国石油集团工程技术研究院建立了全方位长期战略合作,作为该院"钢质管线DGR内外一体化防腐示范基地"和"钢质管线防腐技术试验基地"。公司具有国内首套DGR钢质管道防腐生产线,其中"钢管预补口自动横传系统"、"钢管纵向精准定位传送系统"、"独立弧压自控三维数控专用TIG堆焊固溶机床"等均为国内首创,具有完全自主知识产权。
油田小口径管线DGR内外一体化防腐技术
随着油田采出液腐蚀介质的增多,迫切需要进行管线内防腐处理,以提高管线寿命。钢管内防腐处理后,焊口内补口成为管线内防腐层连续的关键。多年以来,钢质管道内壁防腐工艺中的焊口补口技术,一直是制约钢质管道内壁防腐工艺的技术瓶颈。
1、简介
解决难题:
针对内补口技术限制了内防腐涂层技术在小口径管线上的应用,我们研发了针对小口径钢管的¡°堆焊固溶端头处理+内外有机防腐层¡±的内外一体化防腐技术(简称DGR),实现了工厂规范化生产,可有效解决小口径管线的内防腐难题。
技术专利:
发明专利:钢质管线焊口预补口固溶过渡近电位不锈钢堆焊方法(201710228615.3)
实用新型专利:一种堆焊固溶(DGR)预补口钢管(201720367579.4)
实用新型专利:一种内外熔结环氧DGR复合钢管(201720367205.2)
2、特点、结构及工艺流程
★管体内外涂层和端头内堆焊固熔均在工厂预制完成,质量可控;
★双金属外观界面合金成分及电位渐进过渡;
★管端预补口层与管体内表面平滑过渡;
★管体及固熔过渡区采用熔结环氧粉末;
★管体内壁焊接热影响区防腐由预补口层承担;
★现场焊接完成后只需要做外补口,不需要内补口。
3、预补口工艺特点
★机械加工后进行预补口处理 ★不锈钢堆焊预补口
★双金属外观界面固溶过渡 ★管端预补口层机械加工
预补口层可根据输送介质的成分和腐蚀性,选择镍基合金、双相不锈钢和奥氏体不锈钢等耐蚀合金。
石油工业防腐保温产品质量监督检验中心检验报告
中国石油集团工程技术研究院耐蚀性检测报告
4、现场实验
2016年4月
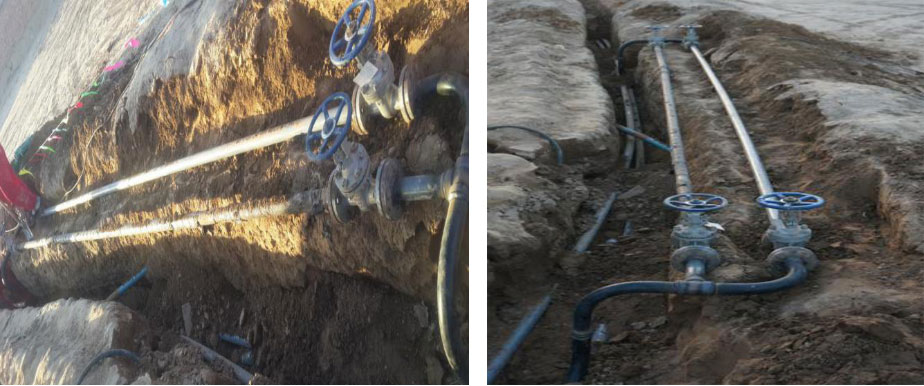
长庆油田采油三厂柳101-252井组
★DGR试验管为Φ60×4mm,共3根,长度分别为1.5m、4m、1.5m,对接焊后管段总长7m,接入集输管线。
★内防腐层:
管体:改性熔结环氧粉末(厚度500~600μm)
端口:耐蚀合金堆焊层(厚度1.5mm,长度65mm)
★外防腐层:熔结环氧粉末(厚度300~400μm)
DGR工艺沿用了耐蚀合金管端冶金内覆结构,克服了堆焊引起的管端缩径缺点,管端耐蚀合金层经过机械加工,充分保证管线组对精度。
DGR工艺通过特殊工艺使管内双金属外观界面过渡区合金成分渐进变化,引起从耐蚀合金层表面至低碳钢基管表面的过渡区开路电位由高到低渐进变化。
DGR工艺的缓坡型过渡区形状不但有利于熔结环氧粉末涂层的有效覆盖,且过渡区各分区可以分别构成复相电极,降低了双金属外观界面的电位差,避免了涂层失效后双金属外观界面腐蚀沟的形成。
在DGR内、外一体化工厂预制防腐施工中,内防腐采用改性熔结环氧粉末二次成膜工艺,相对一次成膜工艺提高了粉末固化率,提高了涂层与耐蚀合金层的粘结能力,保证了涂层在基管和过渡区上的结合力。
利用DGR工艺生产防腐管可以实现工厂化预制,质量可检可控,现场焊接安装后免除了内补口工序且能实现管线内防腐层连续完好;也可以根据介质变化选取不同的耐蚀合金和防腐涂料,能够较好地解决小口径管线的防腐难题。